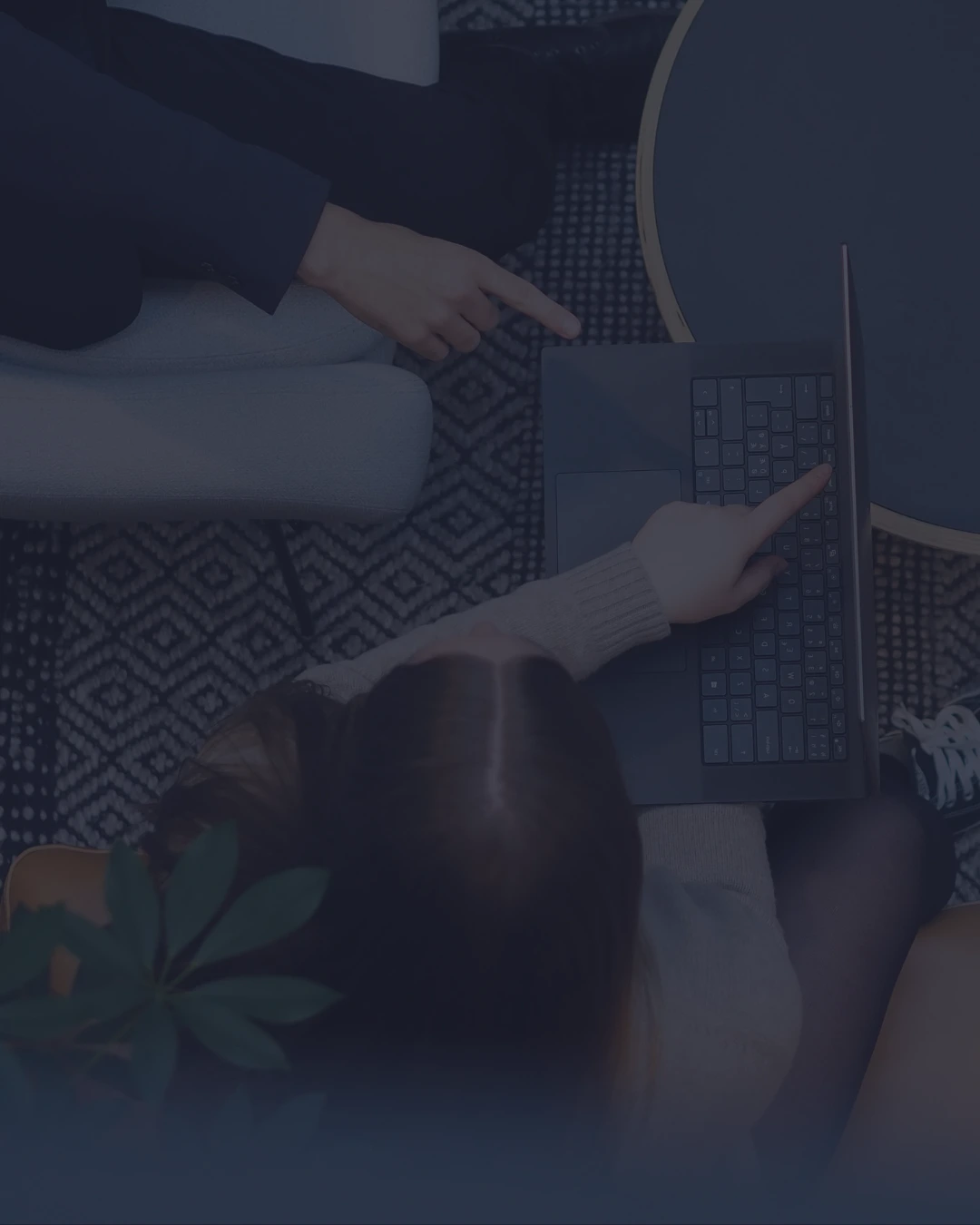
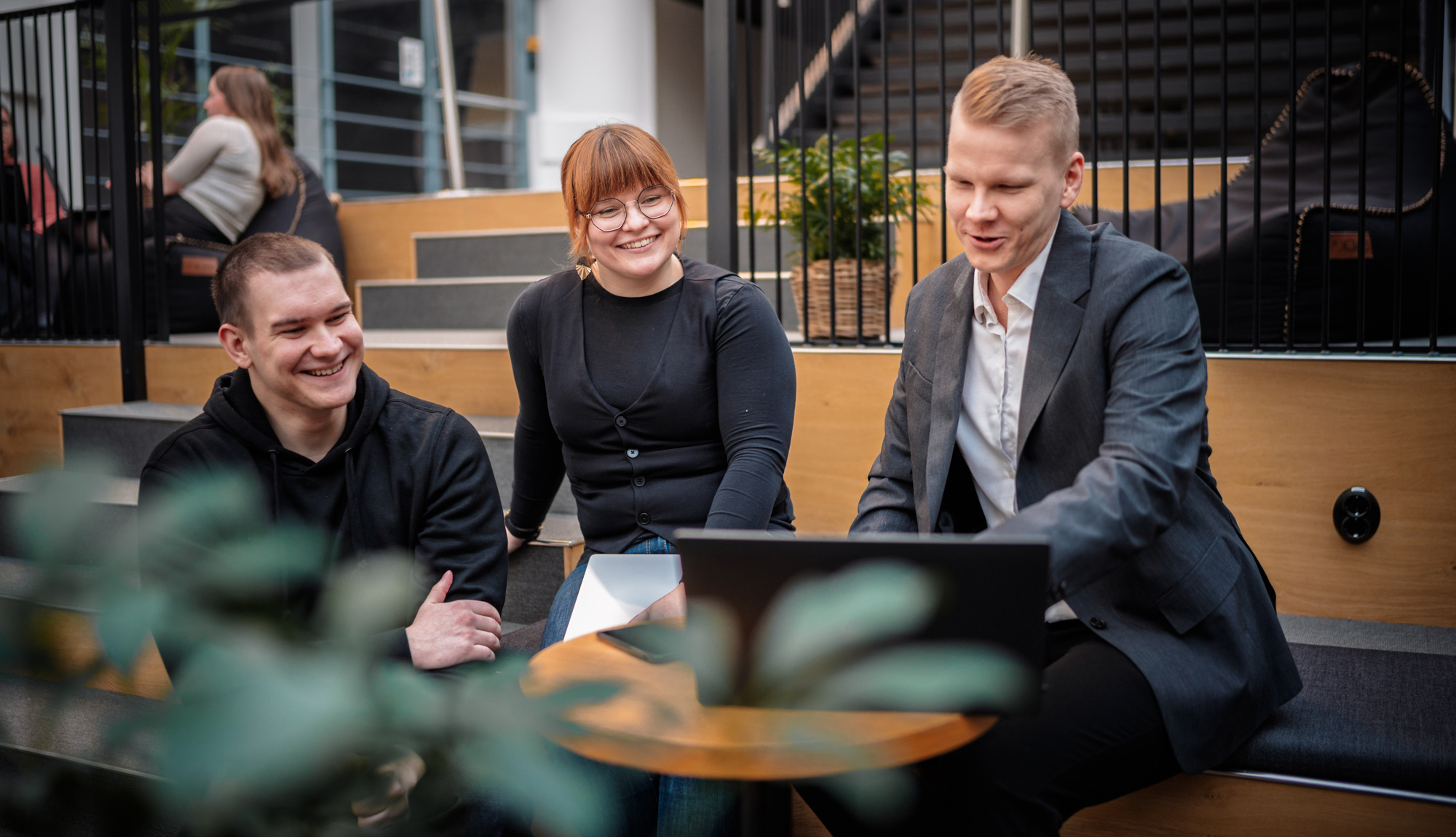
Committed to ease your everyday life
Making your organization’s everyday life easier starts here – get to know our services
Almost 600 software customers trust Arter
At Arter, we believe that a smooth everyday life is the key to success. That’s why we are committed to making your organization’s everyday life easier.
Our core competencies focus on quality management, enterprise architecture, and the development of operational systems, as these areas provide a comprehensive package of tools for both management and continuous improvement of everyday operations.
Contact us and tell us what kind of solution you need help with.
Please also note that Arter has the ISO 27001 certificate.

400+ customers
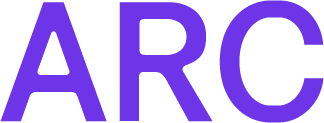
180+ customers
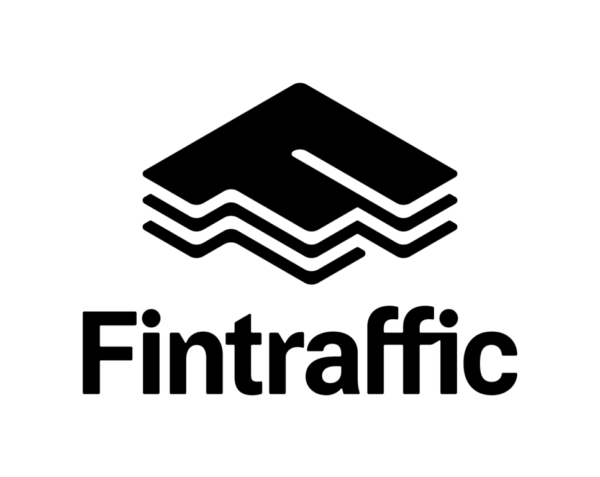
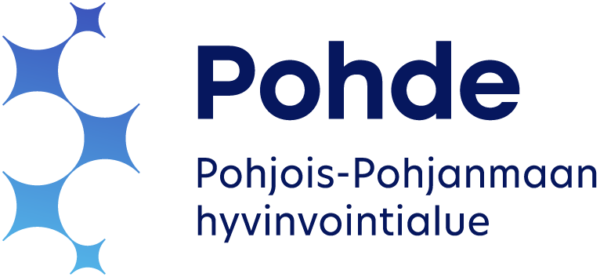
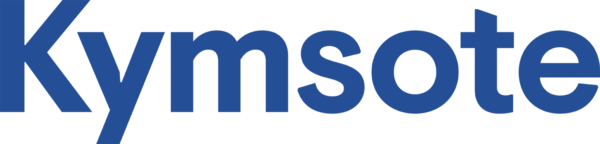
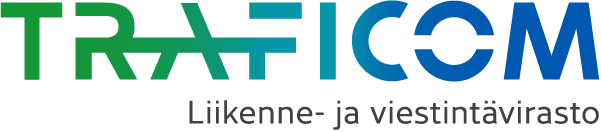
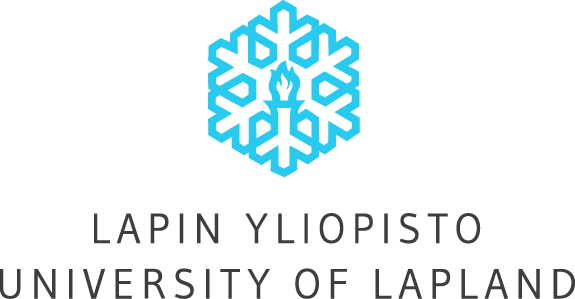
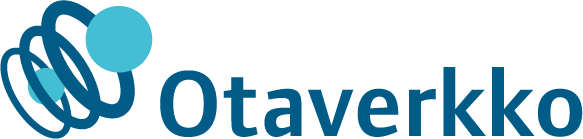
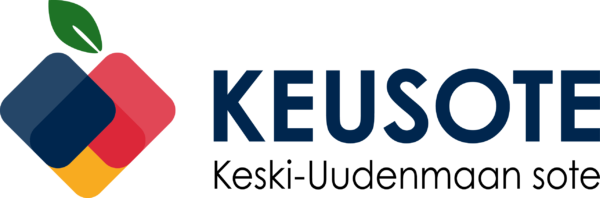
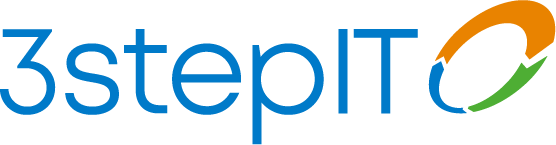
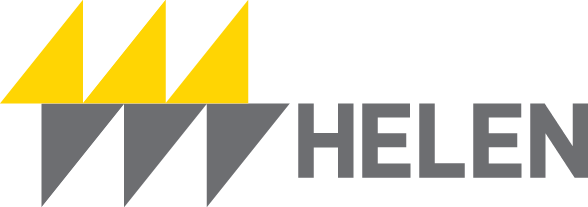
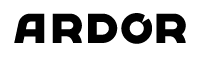
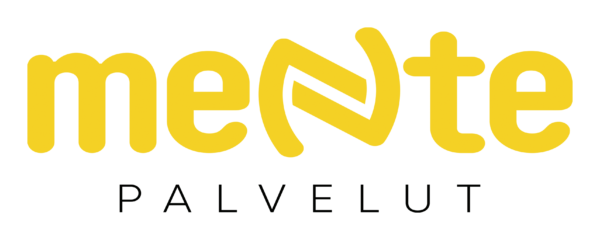
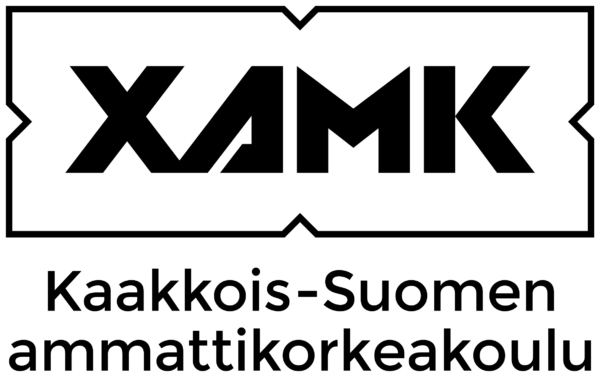
From consulting to concrete actions – experts and software as part of your daily life
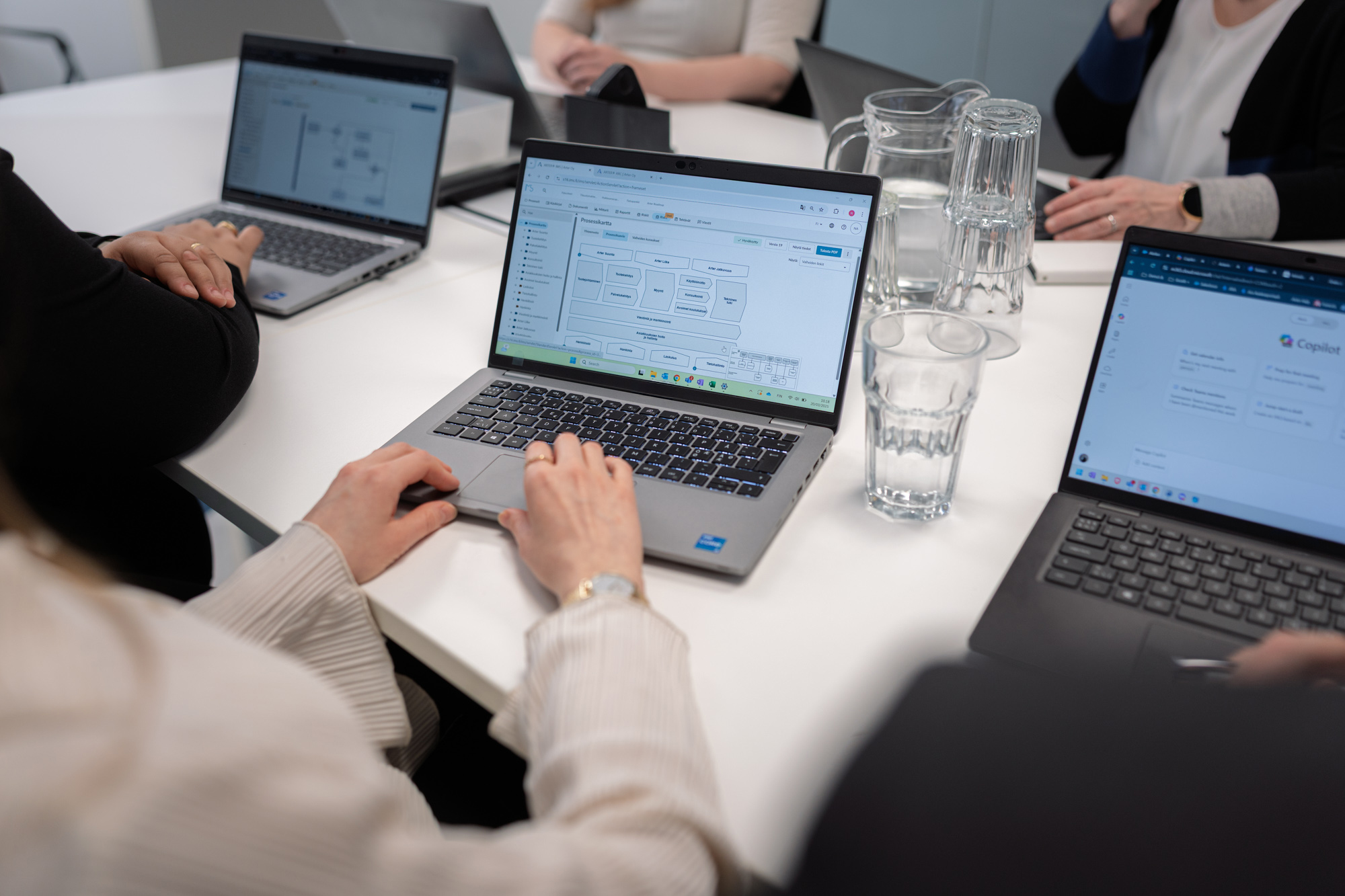
IMS-software
With the IMS software, you can build a quality management, management, or operational system tailored to your organization’s needs, making quality transparent.
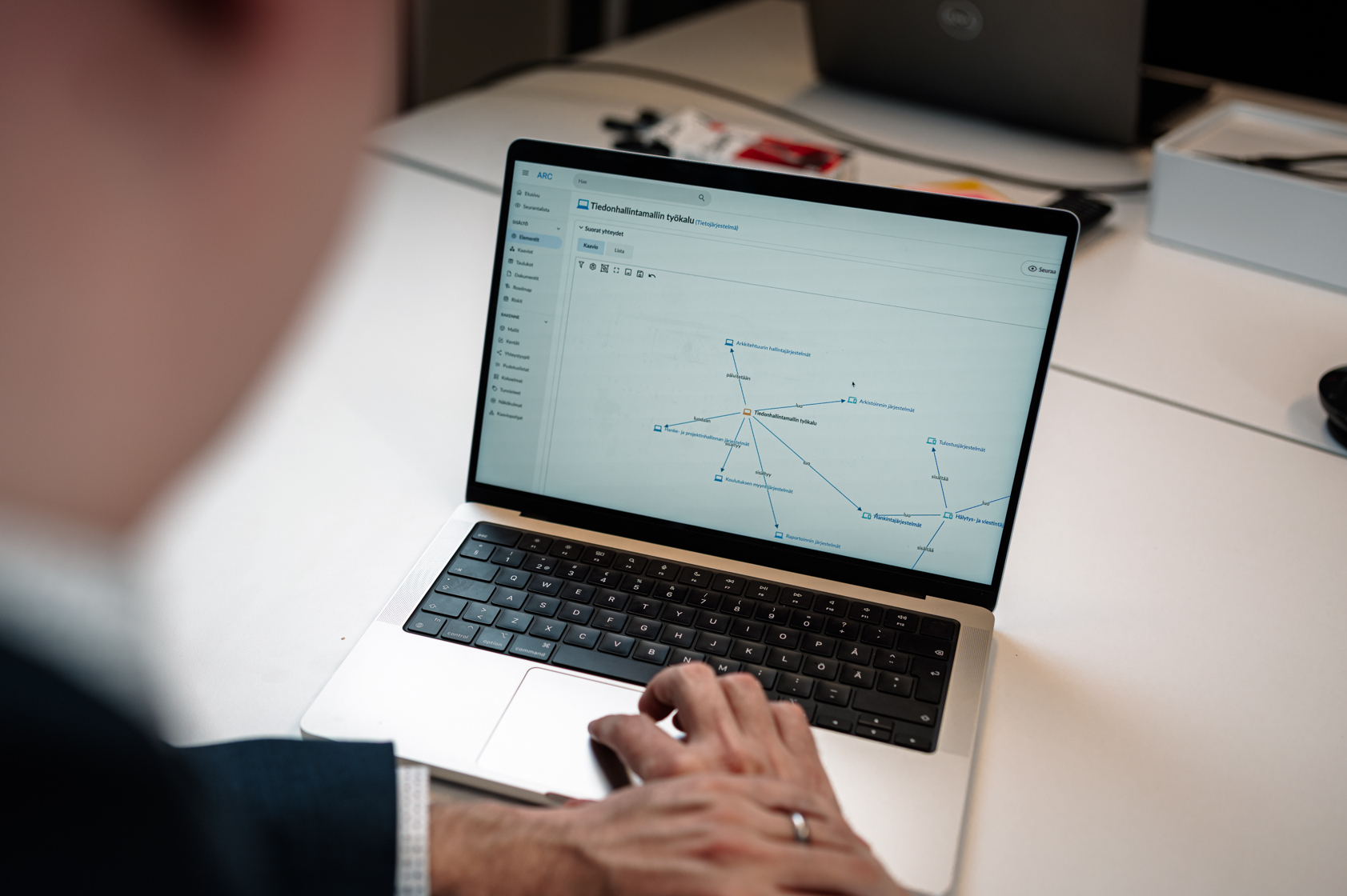
ARC-software
The ARC software is a flexible enterprise architecture visualization tool that allows you to model, document, and maintain your organization’s enterprise architecture descriptions
Free material bank at your service
Information, tools, and tips – all in one place.
Stop struggling – start with the easiest way. Arter’s material bank brings together practical models and tips that truly make your organization’s daily life easier.
-
Published on:
-
Published on:
Documenting processes with The 3-page technique
-
Published on:
What is quality management with IMS software?
How can we make your organization’s daily life easier?
Send a contact request using the form provided.