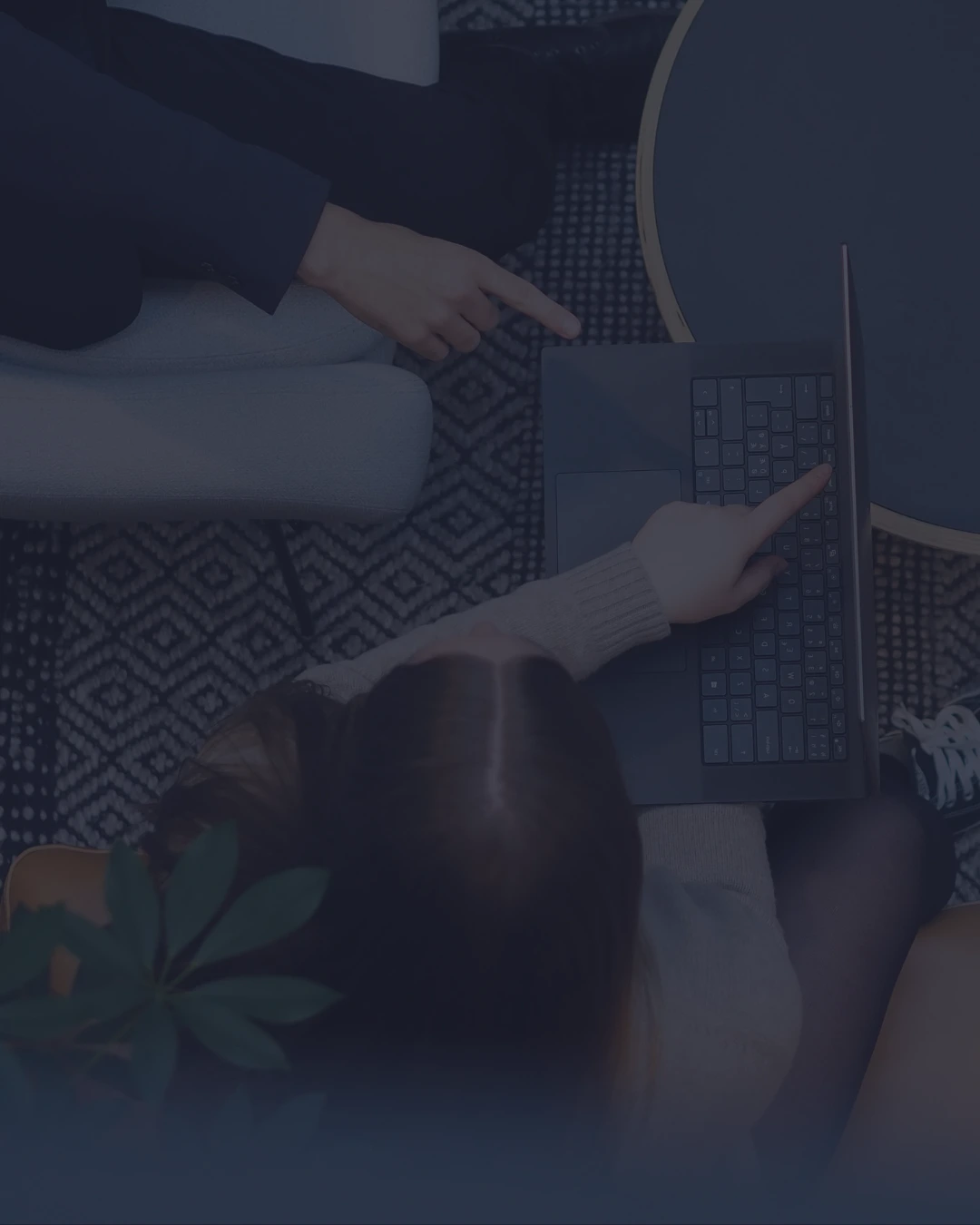
About Arter
Arter was founded in 1998 and employs around 45 experts. Our office is located in Pitäjänmäki, Helsinki. Our core competencies focus on quality management, enterprise architecture, and the development of operational systems. Our business is divided into software development and consulting and training services.
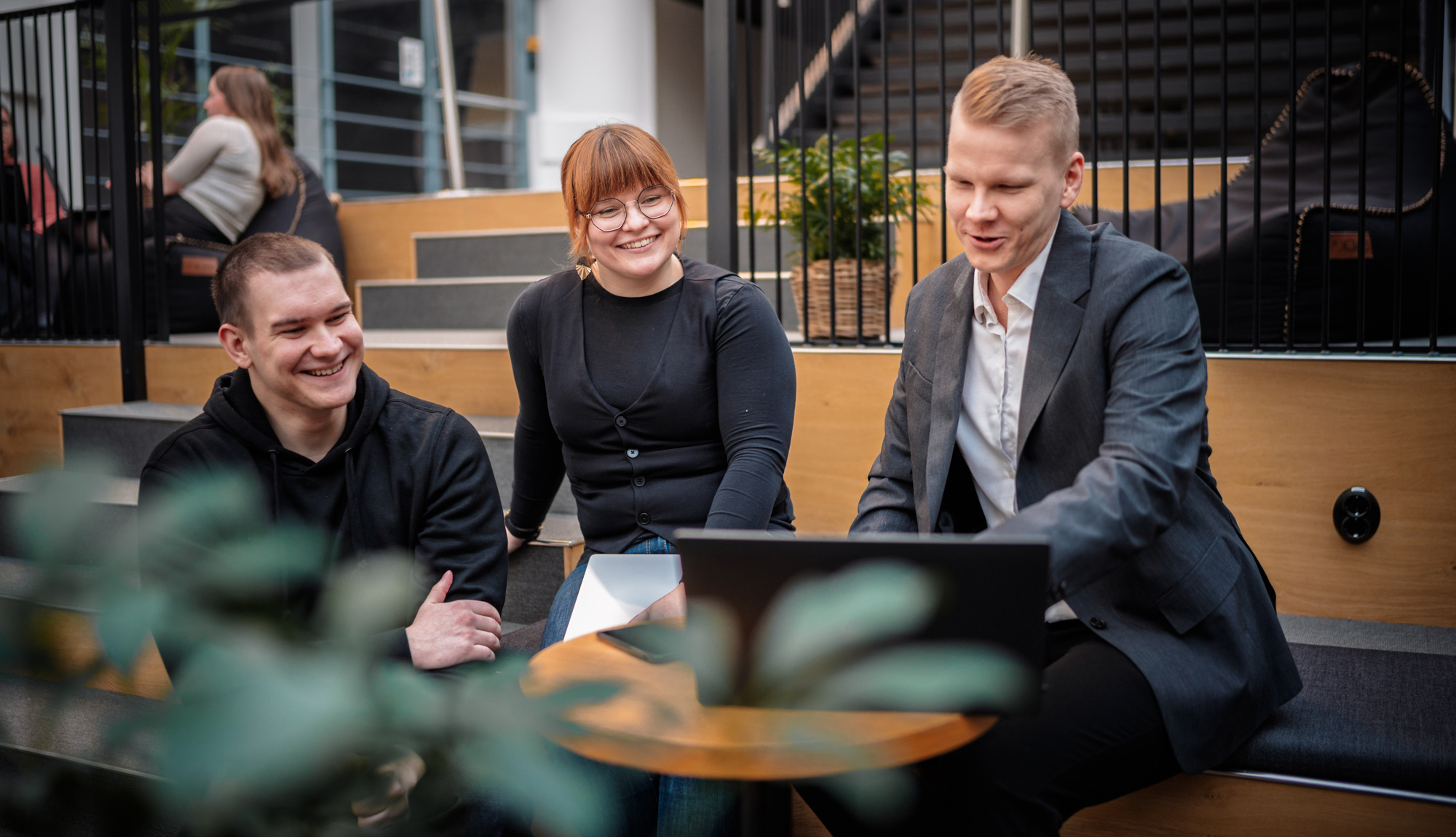
Arter is trusted by nearly 600 software customers
At Arter, we believe that smooth everyday life is the key to success, which is why we are committed to making our customers’ daily lives easier.
Our core competencies focus on quality management, enterprise architecture, and the development of operational systems, as these areas provide a comprehensive package of tools for both management and continuous improvement of everyday life.

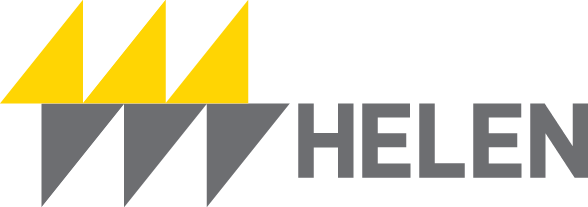
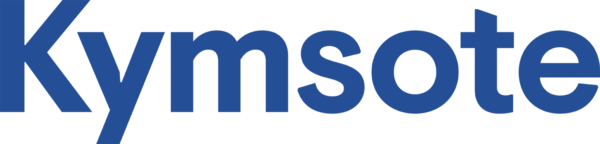
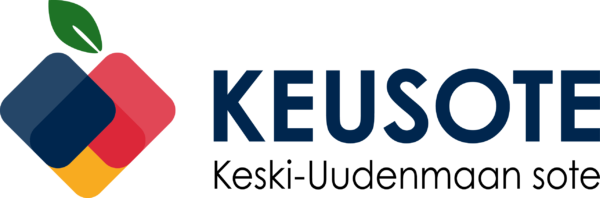
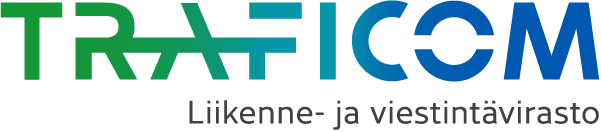
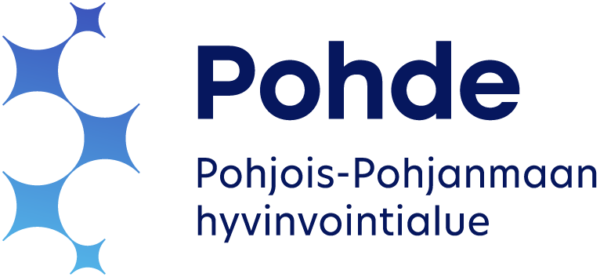
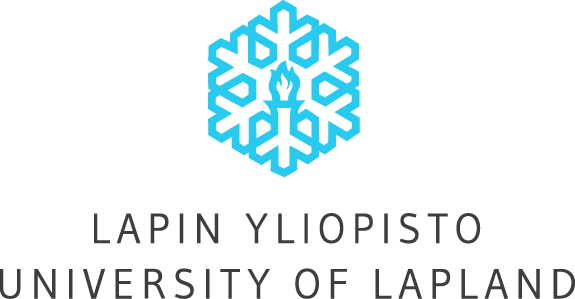

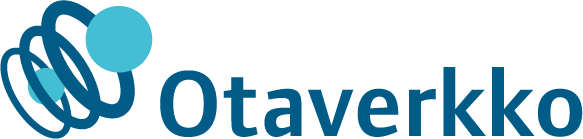
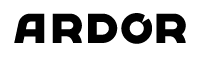
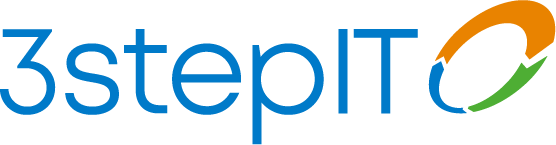
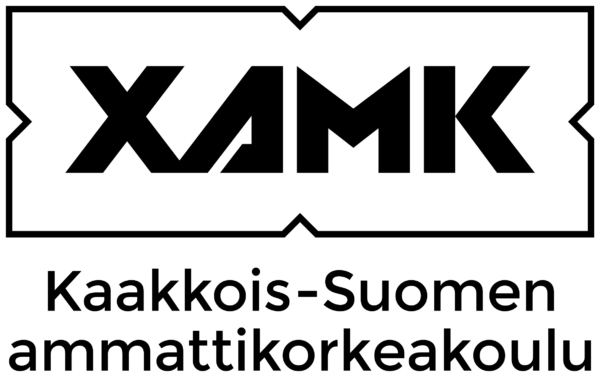
Tutustu Arterin palveluihin
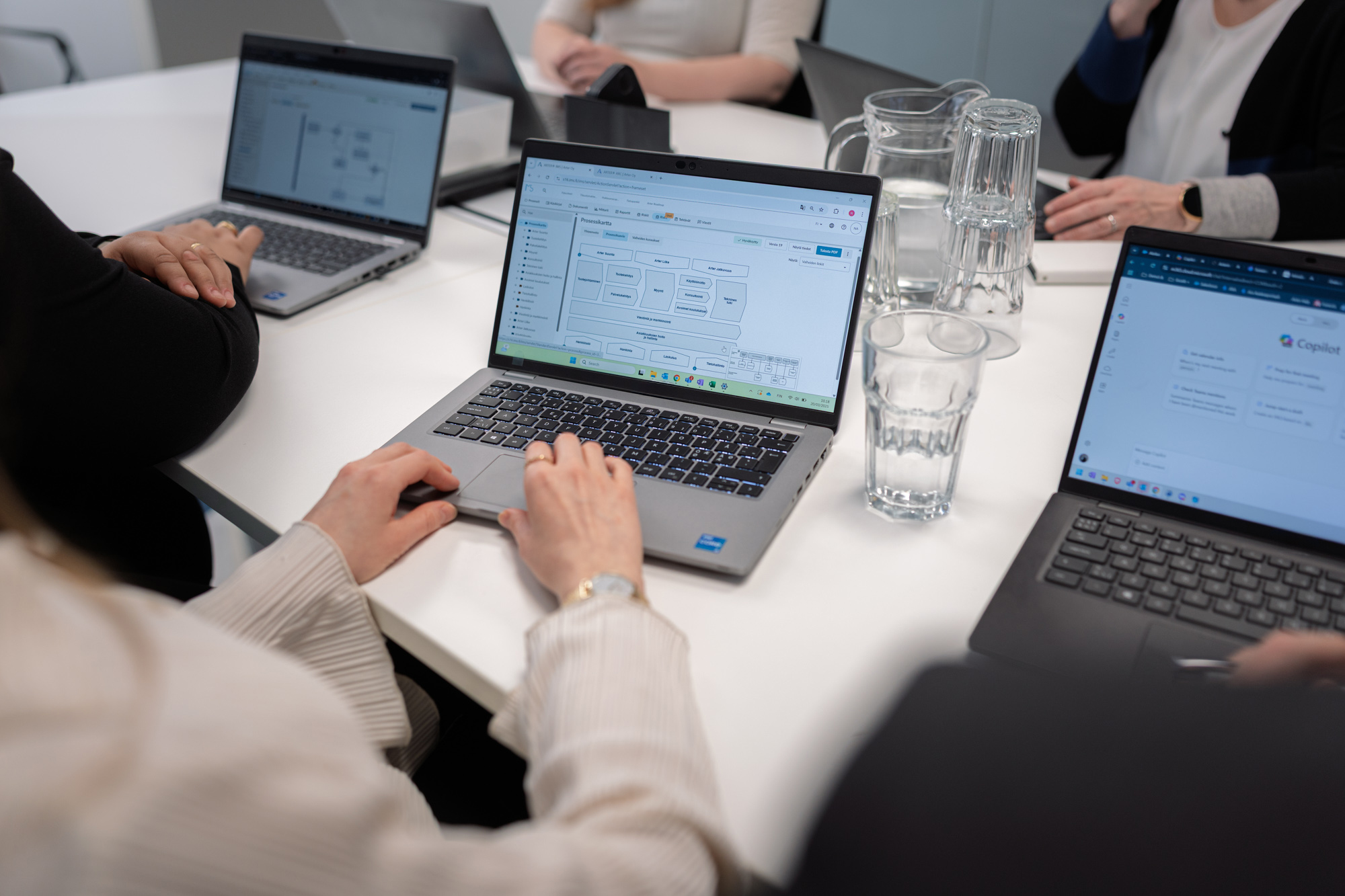
IMS-software
With the IMS software, you can build a quality management, management, or operational system tailored to your organization’s needs, making quality transparent.
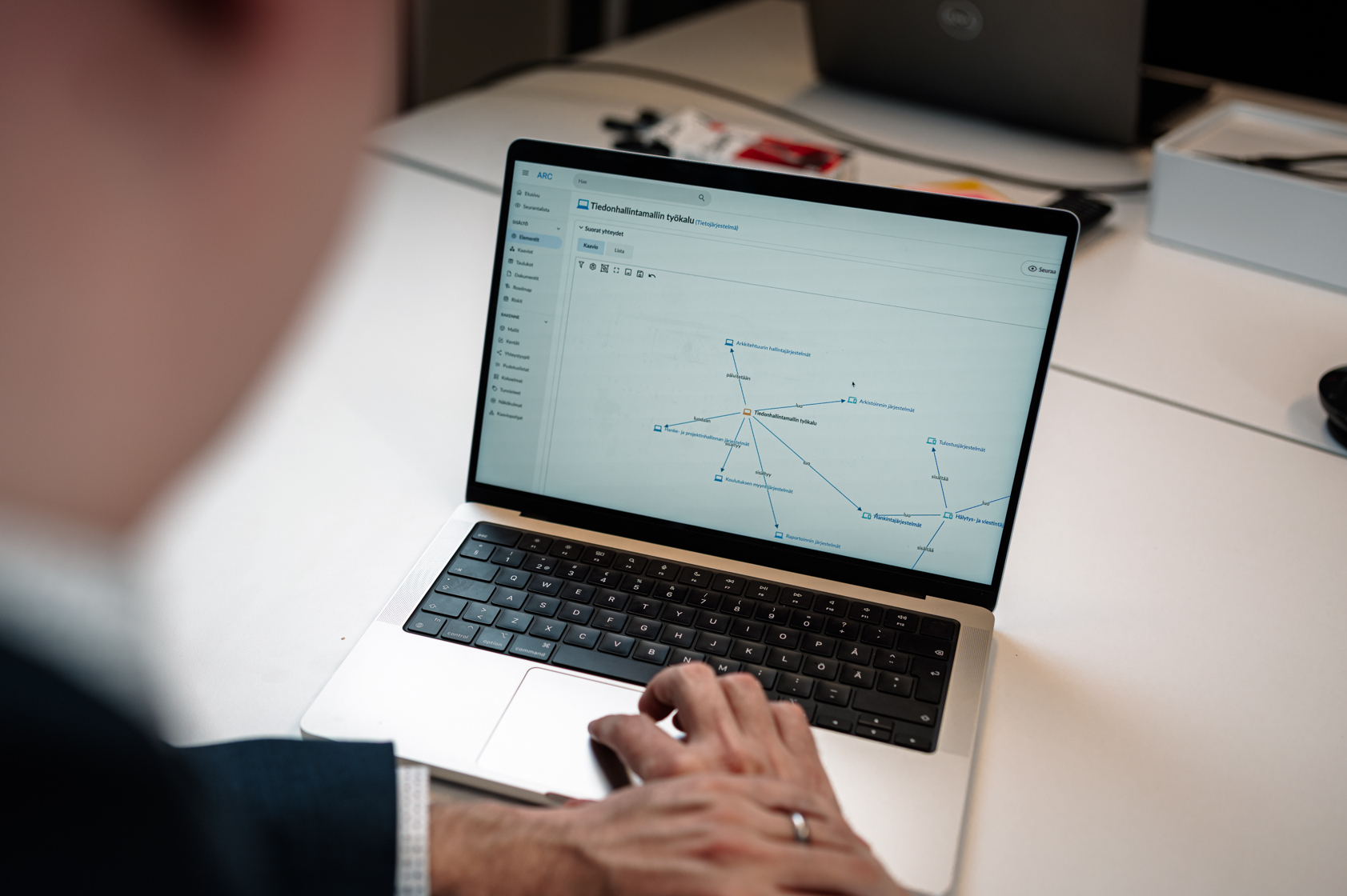
ARC-software
The ARC software is a flexible enterprise architecture visualization tool that allows you to model, document, and maintain your organization’s enterprise architecture descriptions
Arter´s story
In the 1990s, the ISO 9001 standard had just been published, and a wave of quality management system certifications swept into Finland. Our founding members, Ossi Ritola and Jussi Moisio, who worked as chief evaluators at the Finnish Standards Association, started offering quality management training as entrepreneurs. The focus of the training changed over time, but at its core, it was always about developing the customer’s business.
We noticed that customers repeatedly lacked modern tools for business development. As a solution, we programmed them ourselves in Pitäjänmäki, Helsinki, and began offering domestically built software for quality management and enterprise architecture.
Thanks to our strong desire for development, we solve customer challenges today in municipalities, listed companies, and small boat workshops. We do this with a genuine desire to make our customers’ daily lives easier.
Since June 2019, we have been part of the Dutch Total Specific Solutions, which includes nearly 85 independently managed software business units in Europe. TSS’s headquarters are located in the Netherlands, and the company has over 2300 employees in Europe. TSS is part of the Dutch publicly listed Topicus.com group.
In June 2021, Arter was awarded the ISO 27001 certificate. The ISO 27001 certificate is a proof granted by an accredited certification body that Arter Oy’s operations follow good information security principles and that we operate responsibly and systematically in the field of information security.
Explore our expertise through our content
-
Published on:
-
Published on:
Documenting processes with The 3-page technique
-
Published on:
What is quality management with IMS software?