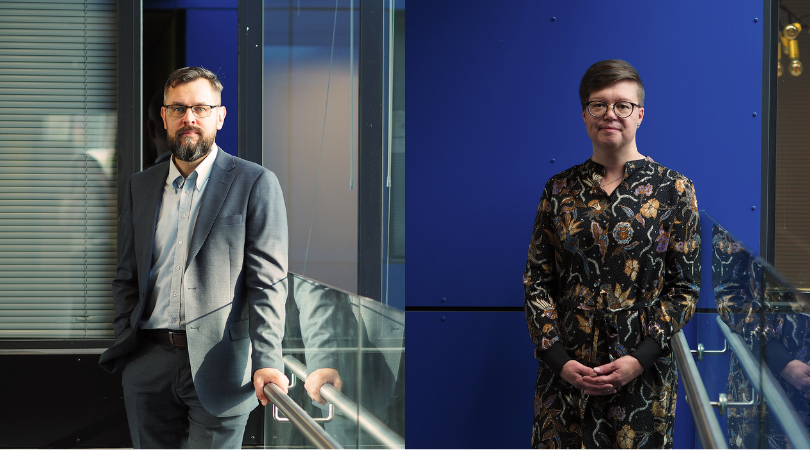
Materiaalipankki
Arterin materiaalipankista löydät inspiraatiota ja konkreettisia vinkkejä laadun- ja jatkuvuudenhallintaan, kokonaisarkkitehtuuriin ja liiketoiminnan kehittämiseen liittyen.
-
-
-
Published on:
Näin viestit laadunhallinnasta selkeästi
-
Published on:
ISO-standardit uudistuvat – katso aikataulu
-
Published on:
Tavoitteena sertifikaatti
-
Published on:
Johdon katselmukset – näin onnistut niiden toteutuksessa
-
Published on:
Laadunhallinnan 7 perusperiaatetta
-
Published on:
ISO 9001 -standardi ja toiminnan dokumentointi
-
Published on:
Uusi laatupäällikkö – ota ainakin nämä asiat haltuusi
-
Published on:
Laadunhallintamenetelmät – suunnittele, valvo ja paranna
-
-
Published on:
Johtamisen rooli toimintajärjestelmän menestyksessä